Pablo Sempere de la Plata
La robótica colaborativa revoluciona las fábricas. Getty Images
Expertos de Danone, Seat o Carbures cuentan sus experiencias.
La robótica y analítica de datos lideran la transformación.
Cuando se habla de industria 4.0 y de la adaptación del sector productivo a la cuarta revolución industrial, suele pecarse de un exceso de maquillaje, quizá de ilusión, en el que el esplendor de la robótica, la inteligencia artificial, el big data o la impresión en 3D, eclipsa los avances reales. “El marketing sigue estando lejos de la realidad, es muy llamativo hablar de todos estos cambios, pero a la hora de la verdad, no es tan fácil adaptarlos a la fábrica”, explicó el socio director de MESbook, Diego Sáez de Eguílaz, durante esta semana, en el marco de la jornada Fábrica inteligente e hiperconectada, organizada por el centro de formación, iKN. Una vez aclarado este punto, lo que sí es cierto es que las fábricas están aclimatándose, a paso firme, a la cuarta revolución industrial.
Utilizar la tecnología para optimizar los procesos y, sobre todo, la toma de decisiones, es uno de los puntos que mayor peso están adquiriendo en las plantas. “En nuestro caso hemos desarrollado un big data enfocado al control de producción. Así tenemos una herramienta clave y fiable para resolver problemas, e incluso poder tomar decisiones alocadas, disruptivas, sin que afecten al total de la cadena productiva”, explicó el director de proyecto de motor eléctrico de la fábrica de Seat y Audi Hungaria (Barcelona), Leandro Pereyra. A esto se le suma la posibilidad de controlar el producto con todos los datos de los que se dispone a tiempo real, algo alejado a lo que ocurría antes, cuando no se sabía si los deberes estaban hechos hasta que el artículo salía de la cadena de montaje.
“De esta forma podemos conocer, antes de que todo haya terminado, si el resultado va a ser bueno o malo, e incluso modificar el proceso si algo no va bien”, desarrolló el ingeniero de investigación y desarrollo de la chocolatera Indcresa, Álex Martínez. Para esto también es útil el machine learning, y así tener presentes todos los factores que pueden afectar a la calidad final, algo que también han hecho en la empresa de cacao. “En nuestro caso hay un entorno y unas variables que repercuten en el producto, como el traslado desde la fábrica o si trabajamos en verano o en invierno, que tenemos que tener en cuenta. Estas técnicas nos ayudan en todo el proceso para que no se escape ningún detalle”, apuntó Martínez, no sin recordar que estos mecanismos también sirven para almacenar información, analizarla más adelante y sacar conclusiones.
El análisis de datos nos ayuda a que no se escape ningún detalle en todo el proceso
Álex Martínez, de Indcresa
Así, desde la industria del motor hasta la chocolatera, estas herramientas, cada una a su manera, facilitan todas las tareas. Y no es el único punto en común que tienen ambos sectores: uno de los asuntos más complicados de abordar es el de dar con perfiles preparados para manejar la tecnología. “Tenemos software y herramientas muy potentes, pero no gente disponible para llevarlas”, reconoció Leandro Pereyra. De esta forma, en el caso de Seat, la solución ha sido promover un máster conjunto con la Universidad Politécnica de Barcelona sobre fábrica digital, con el que formar a los futuros profesionales. Por ahora, tal y como señaló Álex Martínez, hay una dificultad añadida de encontrar perfiles cualificados, debido a la novedad del sector.
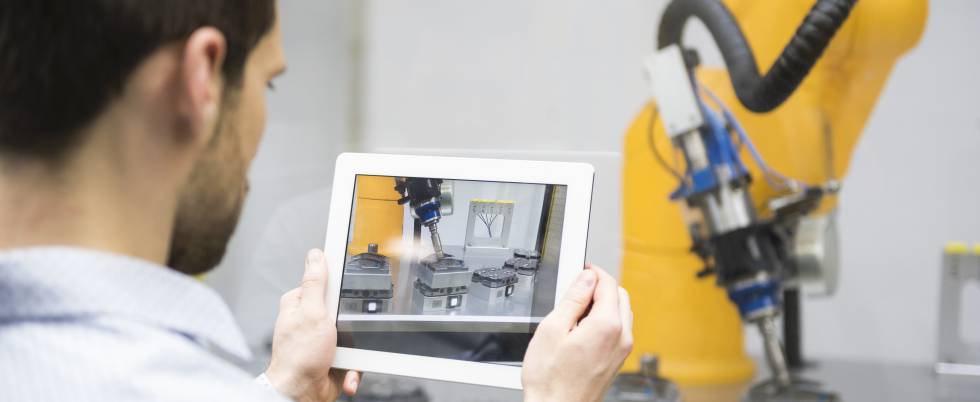
Pero el análisis de datos es solo una de las muchas patas que hay alrededor de la modernización de las fábricas. Otra de ellas, ya obligatoria, es la robótica. De ella tienen buena cuenta en la fábrica de Tres Cantos (Madrid) de Danone, una de las más eficaces de Europa en cuanto al coste de los procesos. Por eso, esta planta es un ejemplo con el que ilustrar las aplicaciones reales que tiene la robótica en los procesos de producción, al menos por ahora. “De momento, solo utilizamos robots en tareas automatizadas, de poco valor añadido, y a veces peligrosas”, prosiguió el director de la fábrica, Alexandre Biau, quien recomendó empezar poco a poco con la implantación de estos avances. “Los primeros que utilizamos fueron en el laboratorio, y de ahí pasamos a otras zonas de la fábrica, como el mantenimiento o la recogida de pruebas en el proceso”.
Se debe tener claro, no obstante, que el robot es una prolongación del profesional, y no un sustitutivo. El marketing y la novedad de estas máquinas también han contribuido a dar alas a la idea de que los empleados ya no serán necesarios, pero al menos por ahora, esa meta sigue estando lejos. “Nuestros primeros robots sirvieron para apilar las fibras de carbono que utilizamos”, ilustró el director de implementación SAP de Carbures, Rafael Repiso, “pero cometimos el error de sustituir al operario. Y hay cosas que la máquina no puede ni sabe hacer. Del robot queremos su fuerza y movimiento; del profesional, su cerebro”. Entre otras razones, continuó el director del departamento de ingeniería mecánica de la Escuela Técnica Superior de Ingenieros Industriales, Antonio Vizán, porque son los propios profesionales los que rápidamente aprovechan el tirón de la robótica: “En seguida sugieren destinos nuevos para optimizar los procesos. Al fin y al cabo son ellos los que saben cómo mejorar sus tareas”.
Cometimos el error de sustituir un operario por un robot
Rafael Repiso, de Carbures
Por el momento, la verdadera transformación se encuentra únicamente en el segmento de la robótica colaborativa, aquellos que son interactivos, fáciles de programar, seguros y complementarios con el empleado. “Son muy asequibles económicamente y hacen mucho más sencillas tareas mecánicas y poco cualificadas”, explicó Alexandre Biau, quien conoce a la perfección estas máquinas, de las que la planta que dirige se sirve para llegar a construir la fábrica del futuro, reto que Danone se ha puesto en el marco del objetivo 2020, junto a otros aspectos como la eficiencia energética y el ahorro de agua y otros recursos naturales.
Pero para poder vivir una transformación total dentro de las plantas, no solo ha de cambiar la mentalidad de las empresas y sus profesionales. También ha de hacerlo la Administración. La impresión en 3D es uno de los puntos que mejor ejemplifican esto. “En cuanto su uso esté regulado y permitido en toda la industria sí hablaremos de una auténtica revolución”, explicó el director general del gigante francés Dassault para Iberia, Nicolas Loupy. Por ahora, las empresas solo la utilizan para modelar, de forma preliminar y al detalle, diferentes piezas, prototipos y artículos, y así conocer con antelación todos los entresijos del producto antes de fabricarlo.
La innovación, a examen
La industria 4.0 preocupa e interesa por igual a las organizaciones. Por eso, la empresa de servicios de ingeniería industrial, Sisteplant, ha elaborado una herramienta de autoevaluación en fabricación avanzada y digitalización con la que las empresas pueden averiguar su nivel de madurez en cuanto a agilidad, robustez, cadena de suministro e inteligencia humana y digital. “Hemos pretendido hacer una evaluación lo más transversal posible para que sea aplicable a todos los sectores y nos permita compararlos con los mismos criterios”, en palabras de la consejera delegada de Sisteplant, Ana Santiago. “Según el FMI, un 88% de las organizaciones reconoce no entender las implicaciones de la industria 4.0 para sus modelos de negocio. Por eso proponemos una evaluación rápida, orientada a identificar el nivel de partida y compararlo con el promedio de la industria, que está en un nivel intermedio, de 2,4 puntos sobre cuatro”.
“Llegará el momento en el que sea la propia máquina la que pida al humano una tarea u otra. Quizá pasemos a convertirnos en personas colaborativas, pero hasta entonces es el profesional el que debe manejar todos estos avances”, apuntó Oriol Fortiá, ingeniero de ventas en AEtech. Es en este punto en el que se encuentra hoy la industria.
No hay comentarios:
Publicar un comentario